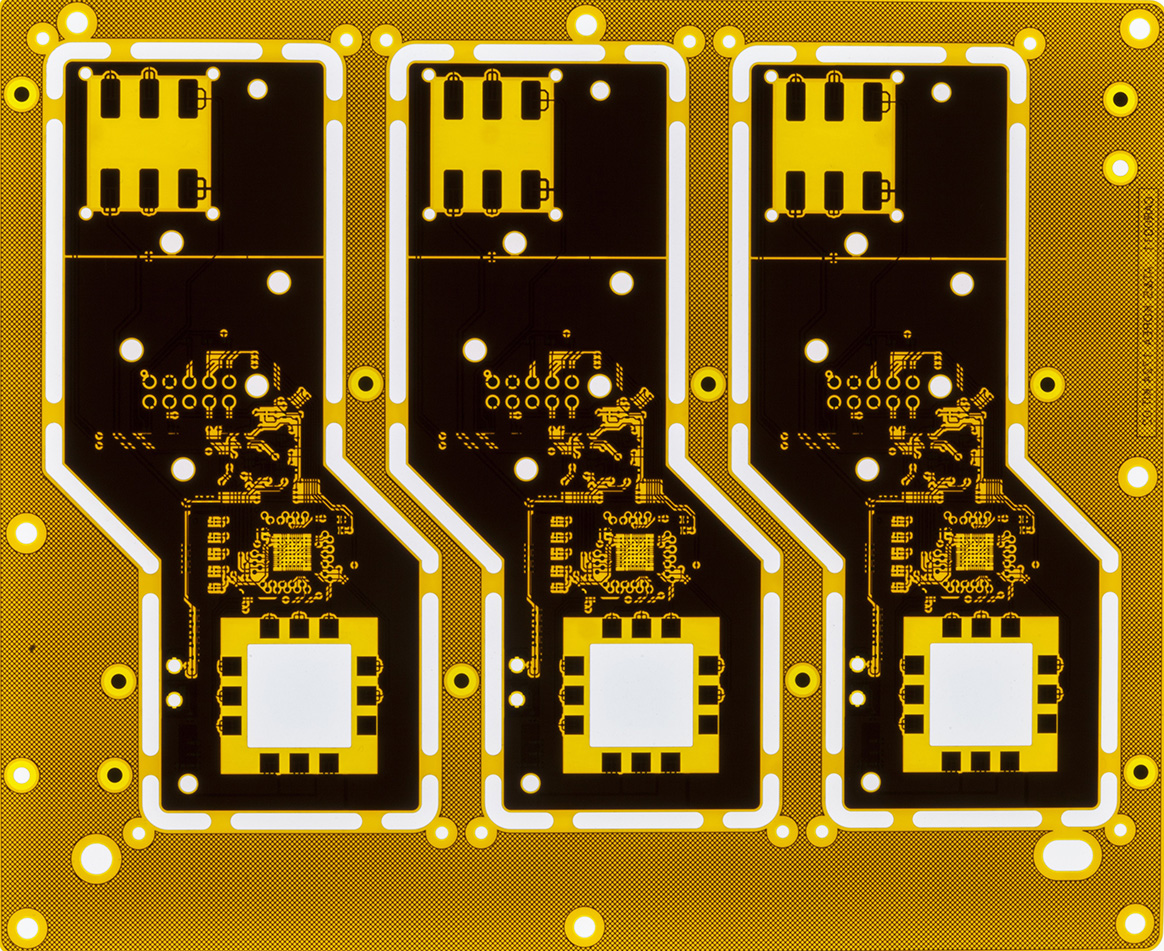
Flexible PCBs offer numerous advantages in design, including greater design freedom, allowing them to fit into tight spaces and complex shapes. They also reduce the number of connections and wiring, improving reliability and decreasing the risk of failure. Their light weight and flexibility make them ideal for compact and wearable devices, helping to reduce overall product weight. They also offer greater resistance to vibration and mechanical stress, improving device durability. Finally, they simplify assembly and manufacturing, reducing costs and lead times. The substrate mainly used for this category is Kapton, a film polyimide.
Our offering of flexible and rigid-flex PCBs is based on the use of the following technologies:
PCB Flex & rigid-flex | Technologies

Flexible
Thin FR4 substrate

Flexible
Kapton substrate

Rigid-Flexible
Rigid-flexible PCB mix
Some technical data
Finished through-hole minimum diameter 100 µm Aspect Ratio PTH = 1:6 or 1:10
Microvia minimum diameter 75 µm (laser drilling) Aspect Ratio blind hole = 1
Fine line minimum track/insulation width 50 µm tolerance ±10%
Minimum Inner layer thickness 50 µm, with 9 µm copper
Minimum Prepreg thickness 50 µm (1 x 106)
Minimum Kapton thickness 50 µm, 25 µm on request
SolderMask/SolderDam glazing or screen printing 100 µm standard and 70 µm on request
Maximum PCB thickness 6.5 mm